Inspection Fixture and Method for Complex Aero Surface
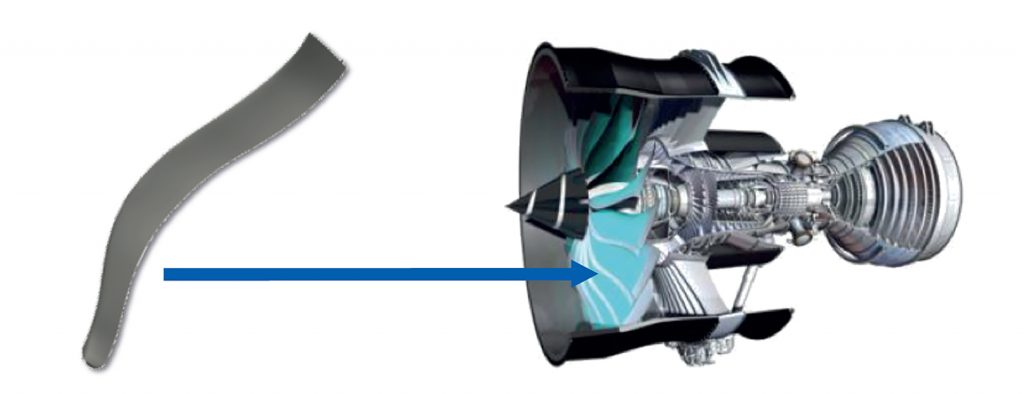
Inspection Fixture and Method for Complex Aero Surface
Verification that the aerodynamic profile is within the Co-ordinate Measuring Machine (CMM) probe-path envelope, using an integrated laser sensor.
Introduction
Gas turbine fan blades have precisely engineered aerodynamic surfaces with geometry directly related to engine performance requirements. It can be difficult to inspect the 3D complex aero-shape, with reliable inspection necessary to confirm that the finished product matches the design intent.
When using a CMM, the part must be positioned reliably, otherwise the probe may collide and require re-calibration.
MetLase was asked to design a repeatable and simple method of locating a complex aero surface for CMM inspection.
Solution
Using the precision laser cutter and joining technology, MetLase was able to design and build a fixture which held the aero section in place and incorporated a laser sensor to verify that the component to be measured would lie within the CMM’s probe-path envelope.
The blade was held securely by distortion-free clamping, enabled by MetLase’s titanium spring technology.
Benefits
The laser incorporated into the fixture showed that repeatable component placement was possible to within ten microns. The design eliminated the time needed for recalibration of the CMM, previously caused by collision of the probe, when the component to be measured was outside the probe-path envelope.
The resulting fixture was thus simple to use, repeatably precise and produced a significant time saving over the previous inspection methodology.
Summary
Delivery: Recalibration time of coordinate measuring machine eliminated.
Precision: Repeatable component placement to within 10 μm (measured via integrated laser sensor) enabled by distortion free clamping and MetLase titanium spring technology.


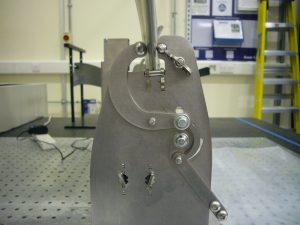
