Case Study
MetLase – Digitally-led & Manufacturing Solutions
COVID-19 Ventilator Design & Manufacture
> The Customer – Ventilator Challenge UK (VCUK)
> The Project – Develop a working ventilator to a new Rapid Manufactured Ventilator Specification (RMVS)
The Challenge
In the early stages of the COVID-19 pandemic, a worldwide shortage of ventilators led the UK government to issue a call to arms to the most innovative companies in the UK manufacturing sector – the Ventilator Challenge UK (VCUK) to quickly develop a working ventilator to the new Rapid Manufactured Ventilator Specification (RMVS) devised by the Medicines & Healthcare products Regulatory Agency (MHRA), to address the current requirements.
The Solution
MetLase knew that meeting the MHRA’s specification would be challenging, so brought together a regulatory compliance team equal in size of their engineering team. Including MetLase’s own compliance lead, and expertise from parent companies Rolls-Royce and Unipart Rail, external contributors included Sheffield Teaching Hospitals, innovation experts CPI and the public health and safety organisation NSF.
Manufacturing and supply-chain activities were led by Unipart Manufacturing, who sourced components and designed production lines within their Coventry
manufacturing facilities.
Additionally, MetLase supported other VCUK partners with design work:
> Meggitt PLC: with the design, manufacturability, and initial production runs of the enclosure for their Spiritus ventilator project.
> Rolls-Royce: MetLase designed and produced 72 bespoke manufacturing workstations in just 10 days, for the new production lines in their Bristol facility, to scale up production of Smiths Medical paraPAC Plus ventilators.
> Cambridge Consultants Ltd: Understanding the detailed workings of a ventilator, and with Unipart Manufacturing’s earlier efforts, MetLase became the preferred manufacturing partner for their Veloci-Vent ventilator.
The Result
The first prototype was tested within 14 days.
MetLase developed their own ventilator, with design emphasis focussed on the availability of components within the supply chain and manufacturability while remaining compliant to the MRHA’s specification.
The Government eventually halted the efforts of all the VCUK consortia companies working on RVMS Ventilators, in favour of ramping up the production of existing products. However, this project demonstrates how MetLase can rapidly mobilise its team of skilled engineers, and apply the patented MetLase technology, which was born out of the aerospace sector, to solve problems across the broadest spectrum of applications.
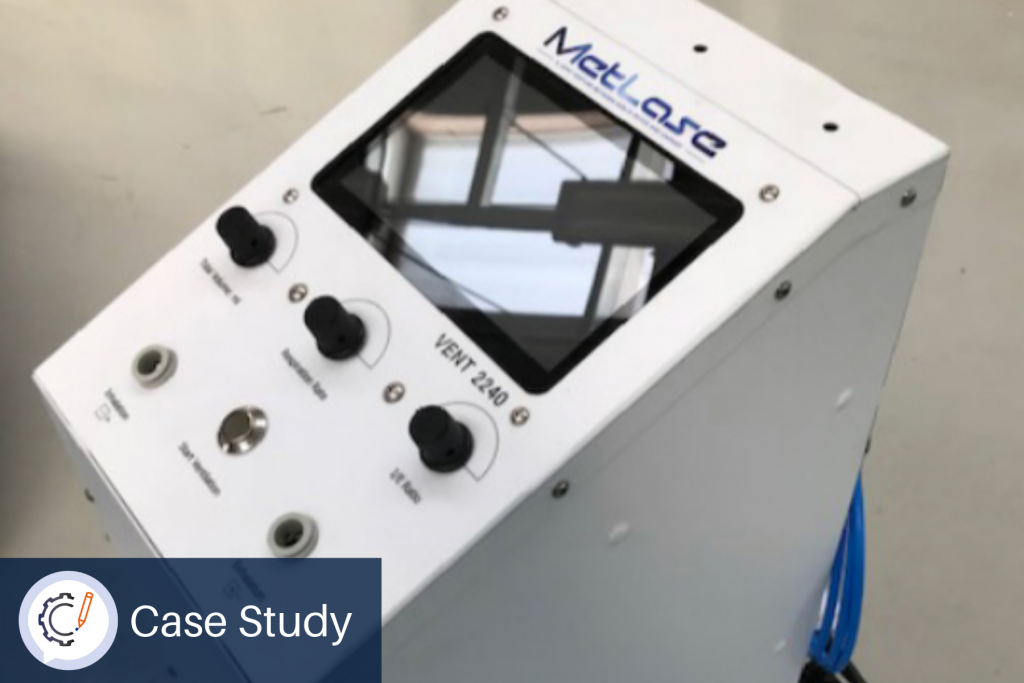
“The Ventilator is a great example of how MetLase can help manufacturing companies adapt to quickly cope with new requirements to keep their people safe and help with any ramp-up as people get back to work”
Steve Dunn
Managing Director, MetLaseSHARE THIS STORY…
More MetLase Case Studies…
