EV Battery Assembly Fixtures
Case Study
Design – Manufacture – Maintain
Revolutionising EV Battery Assembly
Bespoke fixturing solutions solving complex EV battery assembly challenges
MetLase developed an EV battery assembly fixture enabling Hyperbat, one of the UK’s leading manufacturers of high-performance EV battery packs and supplier of batteries for the world’s most powerful production car, to optimise complex assembly operations.
The Challenge
Delivering EV battery assembly precision at speed
Electric vehicles feature multiple battery modules, each comprising approximately 6,000 Li-Ion cells that all require the perfect weld. It is critical that every weld is precise, consistent and safe – any failure can be catastrophic.
Welding electric vehicle battery cells to busbars presents several challenges due to the unique characteristics of Li-ion batteries and the stringent safety and performance requirements in the automotive industry. The tolerance between a successful and unsuccessful weld on a battery busbar is 0.03 mm, so maximum precision is required.
Cells and associated busbars need to be clamped accurately to enable precision welding of the busbars to the positive and negative terminals of all individual cells to achieve effective electrical conductivity. This time-consuming process results in long lead times and operational inefficiencies.
MetLase collaborated closely with Hyperbat’s welding engineers to develop a unique solution to this complex engineering challenge.
The Solution
Working smarter with optimised fixtures and tooling
MetLase designed and, using precision laser cutting and patented joining technologies, developed and built a set of EV battery assembly fixtures that support multiple busbar configurations, automate cell assembly for the first time using deflected beam welding technology to significantly reducing cycle time from 10 minutes to three minutes and increasing throughput by 300%.
The fixtures consist of a lower element to hold a battery module’s frame and the array of cylindrical cells, and an upper element that holds the appropriate busbar.
When assembled, tabs in the busbar are precisely positioned over the terminals of each cell, closing the gap between the busbar and the cells.
This precise positioning allows for automatic welding. To prevent any risk of short-circuiting, key areas of the fixtures were made from non-metallic materials.
MetLase used process gas in the design of the fixture to enable plume removal and uses process gas delivered directly to all processing regions to shielding weld metal during cooling to avoid oxidation of the weld cap.
The Result
Reduced EV battery assembly lead times and optimised efficiency
MetLase’s bespoke solution allowed Hyperbat to transition from manual EV battery assembly to automated assembly for the first time, increasing volume and maintaining precision quality in the process.
The fixtures enabled accurate, repeatable component assembly, delivering:
- 70% reduction in production cycle time
- 300% increase in through-put
- Significant missed weld reduction
- Full project completion in 10 weeks
“The fixtures worked first time without issue. There was no visible beam clipping at the extremities of the PFO deflection, and there was good clamping force – these are world class fixtures and a step forward. “The production cycle time has been significantly reduced, leading to a 300% increase in throughput.”
Dr Nicholas Longfield, Welding Engineering Manager, Hyperbat
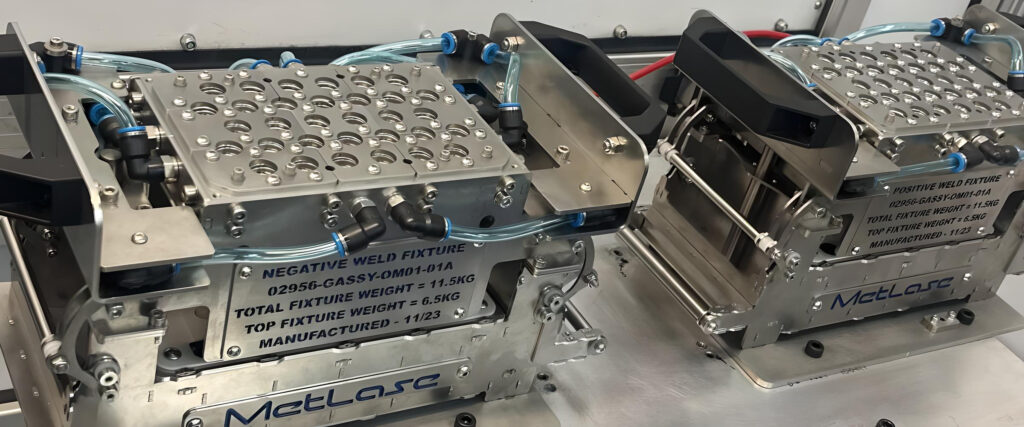
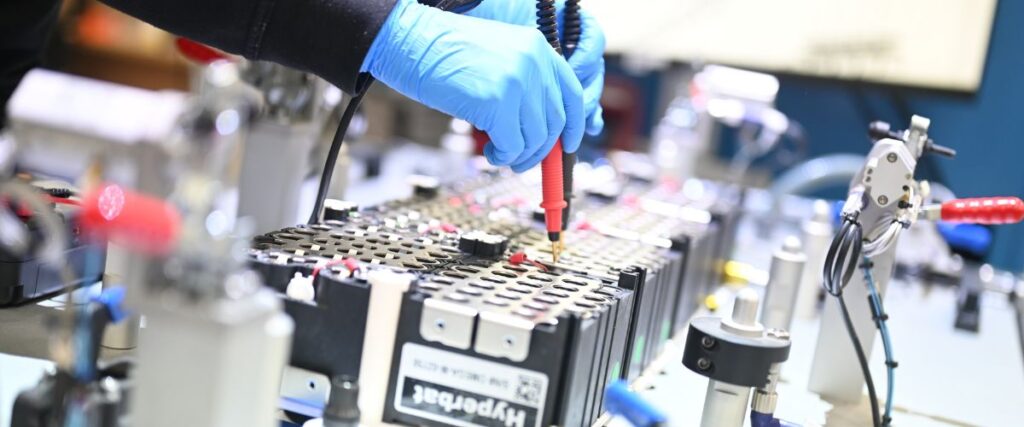
“It’s very rare that manufacturing processes can be improved to this extent, this simply would not have been possible without MetLase.”
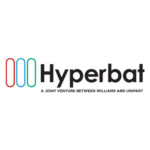
Dr. Nicholas Longfield
Engineering Manager, Hyperbat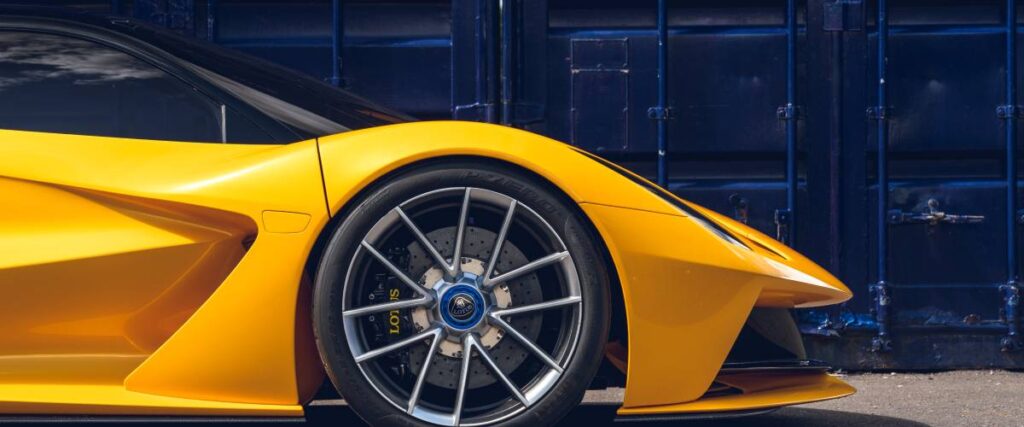
SHARE THIS STORY…
More Case Studies
Need help with your manufacturing or engineering challenges?